- "Silk Road Keqiao · All over the world" into Zhengzhou precision matchmaking conference was successfully held
- Understand the full scene application of roof nonwoven fabric
- Ganzhou textile and garment industry chain and government and enterprise roundtable meeting was held
- Analysis of production technology of woodpulp spunlaced nonwoven fabric
- The 4th Chaoshan International Textile and Garment Expo opened in Shantou International Convention and Exhibition Center
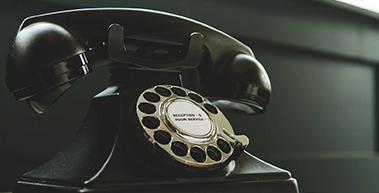
- Cellphone: +86-13430333258
- Email: qdvictorin@gmail.com
- Address: No.95 Kongquehe Wu Road,Jimo Garment Industrial Park, Qingdao City, Shandong Province, China
Woodpulp spunlaced nonwoven fabric is an environmentally friendly nonwoven material made by high pressure spunlaced technology with woodpulp fiber as the core raw material. Its production process integrates key technologies such as fiber treatment, high pressure spunling, functional composite, and has the characteristics of high efficiency, energy saving and environmental protection. The following is a detailed analysis from the core process, technical points and innovation direction:
First, the core production process
Raw material preparation and fiber treatment
Wood pulp fiber selection: Bleached softwood pulp is used as the main raw material, requiring fiber length ≥2.0mm and dust degree ≤25mm/kg to ensure the uniformity and strength of the finished product.
Fragmentation and grinding: The fiber is fully separated by a low concentration hydraulic pulper (3.5%-4.0% concentration), and then the pulp is ground to a beating degree of 28-30°SR to avoid excessive fine fibers resulting in hair loss.
Netting process
Fiber network formation: The wood pulp fibers are arranged into a uniform fiber network by the carding machine, and the horizontal and horizontal strength ratio of the fiber network is improved by cross-laying network technology (controlled within 1.3).
Prehumidification treatment: compacts the fiber network and eliminates air, and commonly uses double mesh clamping or roller prehumidification devices to provide a stable foundation for subsequent spines.
Spool reinforcement
High pressure water jet: The core process uses 20-60MPa high pressure water flow, through the diameter of 0.08-0.15mm water hole vertical impact of the fiber network, so that the fiber winding to form a three-dimensional structure.
Layered composite: ES fiber layer and water-repellent layer (such as polylactic acid fiber + anthocyanin color layer) can be optional to achieve functional composite, meeting the needs of medical and Eisai scenarios.
Post-treatment and dehydration
Dehydration and drying: more than 80% of the water is removed by vacuum dehydration (centrifugal dehydration device), and then the hot air penetration drying (temperature 100-150℃) to stabilize the size.
Functional treatment: including calendering, coating, printing (such as antibacterial treatment) or adding flame retardants to improve surface texture and functionality.
2. Key technical points
Spiny process optimization
Water pressure control: The first stage spool pressure is low (about 60Bar), gradually increasing to 200Bar, and then decreasing to ensure uniform fiber entanglement.
Mesh curtain design: The use of polyester or metal wire woven mesh curtains, aperture and weaving structure affect the surface texture of the product (such as mesh clarity).
Energy saving and environmental protection
Water recycling system: 95% of process water is recycled after activated carbon filtration, reducing energy consumption and wastewater discharge.
Raw material innovation: Renewable fibers such as bamboo pulp and bagasse pulp are introduced to reduce dependence on native wood.
Quality control
Wool loss control: Reduce fiber loss by optimizing the grinding degree, using imported blankets (fineness requirement > 65%), and regularly cleaning the dryer and scraper.
Online inspection: real-time monitoring of gram weight, moisture and defects, combined with intelligent slitting system to ensure product consistency.
The production process of wood pulp spunlaced non-woven fabric achieves the balance of high strength, softness and versatility through precision spunlaced technology, raw material innovation and environmental protection design. With the growing demand for high-performance environmental protection materials in the medical and Eisai markets, its process optimization and function expansion will become the core competitiveness of the industry.
Qingdao Victor New Material Co. Ltd is a professional nonwoven products manufacturer located in Shandong, China. The factory founded in 2013, specified in nonwoven related products(Nonwoven fabrics, Spunlace, Wipes, Roofing Nonwoven)from nonwoven fabric to finished products. We have three major product lines, spunbond, meltblown, and spunlace. Qingdao Victor New Material Co. Ltd offer one stop service from design, manufacturing, packaging, and shipping.
- "Silk Road Keqiao · All over the world" into Zhengzhou precision matchmaking conference wa
- Understand the full scene application of roof nonwoven fabric
- Ganzhou textile and garment industry chain and government and enterprise roundtable meetin
- Analysis of production technology of woodpulp spunlaced nonwoven fabric
- The 4th Chaoshan International Textile and Garment Expo opened in Shantou International Co
- Wood pulp spunlaced non-woven fabric: multi-field innovation driven by environmental prote
- From the hot topic of the two sessions to see the development of new quality of textile in
- Unlock nonwovens: Passwords for a wide range of applications from medical to agriculture
- Spunlace non-woven technology revealed
- The 17th China International Industrial Textiles and Nonwovens Exhibition (CINTE24) came t